4 Common Air Compressor Problems [With Solutions]
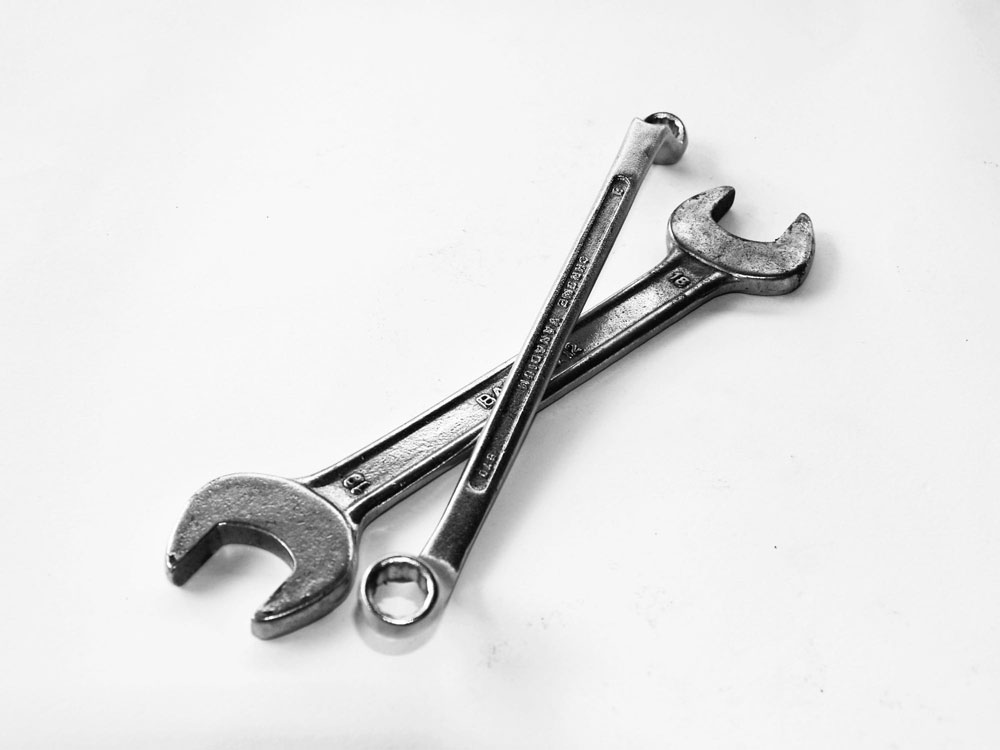
Air compressors are an expensive, integral component of most facilities’ everyday operations. When your air compressor starts acting up, you lose time in production, which means a loss in profits. Like any piece of machinery, there are a few problems that we tend to see often with air compressors, and that have easily accessible solutions. If you want to increase the lifespan of your compressor, here are the solutions to 4 common air compressor problems to check for often at your facility:
Problem #1: Compressor Is Constantly Leaking Air
If your air compressor is leaking air, it’s an issue. Air leaks are a top cause of excessive energy usage, and it also means your compressor isn’t able to function properly. You’ll know your air compressor is leaking when you shut it down and see that the pressure gauge indicates a drop in pressure. You might also have problems with the air compressor failing to shut off and stay off, because it’s compensating for the consistent loss of pressure.
To solve a constant air leak, you have to find the source of the leak and fix it. The best way to find air leaks in your compressed air system is to either:
- Listen for air leaks. When your air compressor is running, take a walk around your plant. Any hissing sounds you hear are indications of an air leak. Connection points are a common culprit, but you may also find leaks along hoses.
OR
- Look for air leaks. If you’re having trouble hearing your air leak, take a few minutes to apply liquid soap to the connections, couplers, and pressure switch, while the compressor is unplugged. When you start it again, keep a close eye to see if you notice any bubbles forming. Those bubbles indicate a leak.
If neither of these methods turns up air leaks, take a look at the tank check valve. If it’s failing to close completely, it could be the cause of your drop in pressure. Inspect the tank check valve — it may need to be cleaned or replaced.
Once you’ve located the source of your compressor’s leak, take steps to fix it. We’ve written an article about How to Stop Air Compressor Leaks to help guide you through it.
Problem #2: Air Compressor Won’t Start
While problem #1 often causes air compressors to run constantly, another common problem is when you can’t get your air compressor to start at all. There are a few reasons this can happen, so it’s easiest to run through this troubleshooting list from the simplest to most difficult fix.
- No Power. Make sure the compressor is plugged in and power is on. If it’s still not working, push the reset button.
- Low Oil. It’s easy to forget to change the oil on an air compressor, but the results can be dramatic. (That’s why we always recommend a regular service schedule.) If your air compressor won’t start, and power isn’t the problem, check and change the oil.
- Power Switch Failure. If your air compressor won’t turn on, there could be an issue with the power switch itself. A simple adjustment to the pressure switch should be able to fix any lack of contact between the pressure switch and the inner circuitry.
- Pressure problem. Your air compressor also won’t turn on if the tank pressure is too low in relation to the cut-in pressure. This is easily fixed by either adjusting the pressure switch or replacing it with one with a lower cut-in PSI.
Problem #3: Air Compressor is Too Loud
Air compressors, depending on the kind you have, are inherently loud machines. But, if you notice your air compressor is making a lot more noise than usual, know that this is a common problem you can probably troubleshoot. Here are a few reasons your air compressor is making an excessive amount of noise, and how to fix it:
- Loose parts. Any loose component in your air compressor will contribute to louder noise during operation. Take a minute to tighten any loose components like the pulley, flywheel, belt, belt guard, cooler, clamps, or any other accessories. Then, check to see if the noise is gone.
- Pistons hitting valve plate. If the air compressor’s piston is hitting the valve plate, you’ll hear a whole lot of noise. Take out the cylinder head and check for any dirt or debris on the piston. Once it’s clean, replace the gasket and reattach the head.
- Crankcase problems. The crankcase is another common culprit for a noisy machine. Check the crankcase. Does it look old and worn out? Replacing the oil or bearings can help, or it may just be time to replace the crankcase outright.
- Improper floor mounting. If your air compressor isn’t properly and tightly mounted to the floor, it’ll make all kinds of noise. Check to see how vibration pads are weathering. If they’re worn, replace them. Tighten the bolts on the compressor as well to make sure it’s securely mounted to the floor and can’t move around.
Problem #4: Excessive Oil in Compressor Discharge Air
This is a common air compressor problem that can seriously affect your daily operations. When too much oil is aerosolized by the compressor’s discharge, it can damage pneumatic tools and accessories, or negatively affect the quality or your production. Luckily, this is a common problem that’s easily solved. Here are a few reasons you might have too much oil in your compressor’s discharge air:
- Restricted intake. When intake filters wear out, they can restrict the compressor’s air intake, causing oily discharge. This is easily fixed by simply cleaning or replacing intake filters.
- Worn piston rings. Piston rings should be replaced periodically. When they’re not, they can cause a range of problems, one of which is oil in your compressor’s discharge air. Replace those piston rings to fix the problem.
- Overfilled oil tank. If there’s too much oil in your compressor, some of it can seep into the discharge. Never fill your oil tank over the “full” mark displayed on the gauge. If this is the problem, just reduce the oil level to that “full” mark.
- Wrong oil viscosity. Your compressor’s oil viscosity should match the requirements of your compressor. If it doesn’t, it’ll end up in your compressor’s discharge air. If this is the problem, empty the oil tank completely, and refill with a different oil of the proper viscosity.
- Inverted piston rings. Upside-down piston rings indicate that the crankshaft is starting to go. They also contribute to oily discharge. Check the piston rings. If they are inverted, it’s probably time to replace the crankshaft.
All four of these common air compressor problems are items our service team sees every day on the road. If you keep running into problems with your air compressor, especially common problems like these, you might benefit from a regular maintenance program that checks for and troubleshoots all of these issues on a regular basis.
If you’d like to get ahead of common air compressor problems and avoid the expensive troubleshooting time that goes with them, the team at TMI can help. Our trained, certified technicians can put your compressors on their schedule to service regularly, so issues like these are far less common. And if you do experience a problem, our team of engineers is available to diagnose your system’s problem 24/7. For maintenance programs or emergency service requests and rentals, get in touch with TMI Compressed Air Systems today.
Contact TMI Air Compressors